Scrap tires present a great environmental threat, but also a profitable business opportunity. Via a pyrolysis process, it is possible to recover partially-renewable oil, steel wire and carbon black from waste tires, which presents great economic opportunities. With the latest tire pyrolysis plant technology, it is possible to convert waste tire into oil and all of those aforementioned commodities via a zero-pollution process.
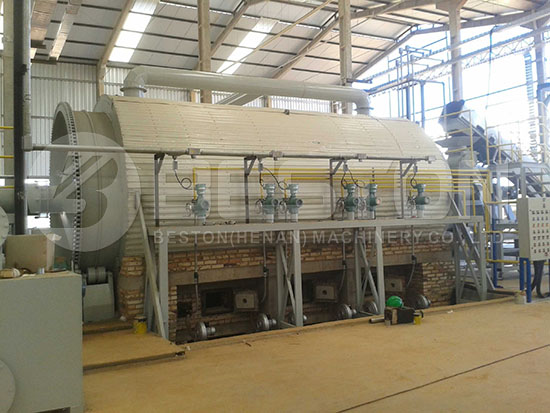
It is estimated that there are over thousands of dollars worth of value in one ton of waste rubber tires. That value is just waiting to be recovered with the aid of tire to oil machines. With such machines, waste tires are shredded and then heated in an oxygen-free chamber (pyrolyzed) for a set period. This converts all tires to fuel oil and combustible gas while leaving behind the original carbon black and steel wire. One ton of scrap tires contains approximately 350-450kg of oil, 300kg of carbon black and 100kg of steel.
It’s important to note that there are different types of pyrolysis plants available, including batch, semi-continuous and continuous. Different models are designed for the use cases and raw materials of different customers. Continuous tyre pyrolysis plant is designed for processing hundreds of tons of waste rubber each week at a facility that operates 24/7.
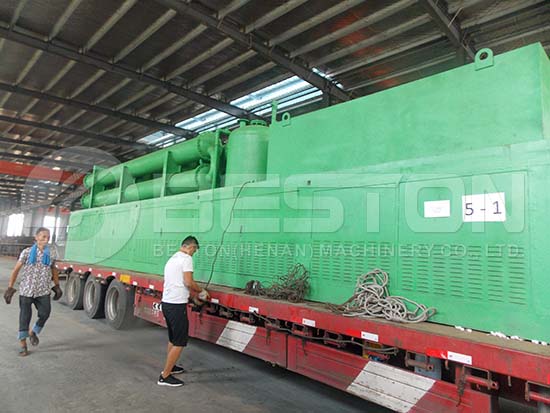
Let’s take a look at the specifications of one of the most popular fully continuous pyrolysis plant from Beston Machinery: the BLL-20. The BLL-20 has a daily capacity of 20 to 24 tons. It takes up a floor area of 45m x 25m x 10m and has a total power rating of 71.4Kw/h. The reactor of the BLL-20 has a diameter of 1.4 meters and a length of 11 meters. It has a horizontal and rotary pattern design. The types of heating materials that can be used to fuel the reactor include fuel oil, LPG, natural gas, wood, charcoal, etc. The plant can be used to process oil sludge, waste plastic, and general rubber waste in addition to used road tires. The life span of the BLL-20 is stated as 5-8 years on the specification datasheet and the model utilizes a water cooling design in the condenser system. More details can be found: https://wasterecyclingplant.com/continuous-tyre-pyrolysis-plant/.
When it comes to the price of continuous tire pyrolysis plants, there are many different parameters that come into play. Some of the cheapest plants are available from overseas suppliers who have access to lower-priced raw materials and a cheap labor market. You will find many high-quality tire to oil machines for sale from manufacturers in China. Many people are shocked to discover that even when global shipping costs, import taxes, and currency conversion fees are taken into account; domestic suppliers can’t compete on price and quality with Chinese pyrolysis plant manufacturers.
The good thing about investing in a continuous tire pyrolysis technology is that the ROI rates are very high and very fast. What’s more, the green tire recycling industry is only set to grow in the coming decades as more countries look for environmentally friendly ways to deal with mounting rubber waste.